Weathertightness remediation work is often characterised by unexpected discoveries in the building fabric once the cladding is removed, even when due diligence is undertaken.
Additional remediation work can inevitably result in extended project timelines and an escalation of project costs. While this is sometimes unavoidable, it’s the way these issues are dealt with by the project team that can make all the difference to the client and project success.
Prendos was engaged on one such project on a nine-storey, 42-apartment building recently. Our Wellington-based consultant Chris Ross acted as both project manager and building surveyor for the project. The dual function of our service for complex remediation projects always strengthens the outcomes of these projects and is appreciated by both the clients and contractors we work with.
Many of the residents opted to remain in the building while work was underway, which added to the project’s challenges, especially as all external walls had to be entirely rebuilt due to the extent of deficiencies found once the cladding was removed. Thanks to the project team’s experience with this type of work, this was thoughtfully managed to minimise disruption to residents as much as possible.
As part of the remediation work, the client – following our advice – opted to reconfigure the interior spaces to some apartments, removing balconies that were seldom used in the prevailing weather conditions. This created more functional space and also improved the value of apartments.
Work began just prior to the outbreak of Covid-19 in New Zealand. With international supply chains becoming increasingly unreliable, the project team quickly identified significant programme and cost risks, and proposed alternative solutions to mitigate or eliminate them. Commencement was deferred to allow materials to be brought in from overseas and stored, rather than anticipating on-time delivery once work was underway. Careful analysis of the raw materials supply chain for certain components revealed significant risks. As a result, we were able to assist the client with making an informed decision to specify a New Zealand supplier for their joinery and to undertake design amendments. Although additional costs would be incurred, this removed significant risk from the project.
Fire and structural improvements were also required, and existing mechanical ventilation systems had to be adapted for remediation. Exceptional coordination between the design team, contractors and suppliers demonstrates the success of value engineered solutions without sacrificing functionality.
Alongside these challenges, Prendos also managed negotiations with neighbouring properties and assisted with the development of property encroachment licences. This also required us to prepare a detailed access plan that was fundamental to agreeing access terms.
Although this was a hugely challenging project in many different ways, the outcome for the client was positive. While there were areas of scope creep, the effects were minimised as much as possible thanks to the experience and technical understanding of the project team.
Client testimonial
“I’m very pleased to endorse the work that Prendos do”
“…and I can say with confidence we were well looked after. I was impressed with the way questions and frustrations around the ongoing work and cost escalation were dealt with. The project went on for several years, and for those of us who did stay it created frustrations, but our Project Manager’s calm responses and presentations to the committee were well received and helped to calm the anxieties.
“The good relationship between Prendos and our Quantity Surveyor also gave us confidence, and together they advocated on our behalf to MBIE to our considerable advantage which we appreciated.“
Henry Stubbs – Body Corporate Chair, 5 Kent Terrace
Photo credit: Kevin Hawkins Photography.
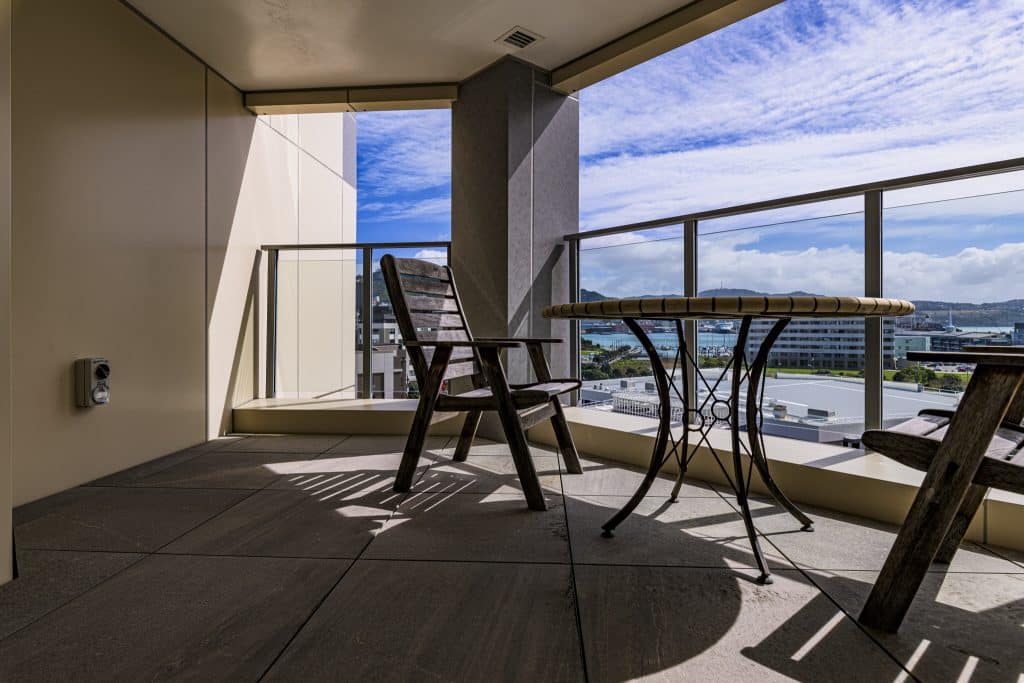
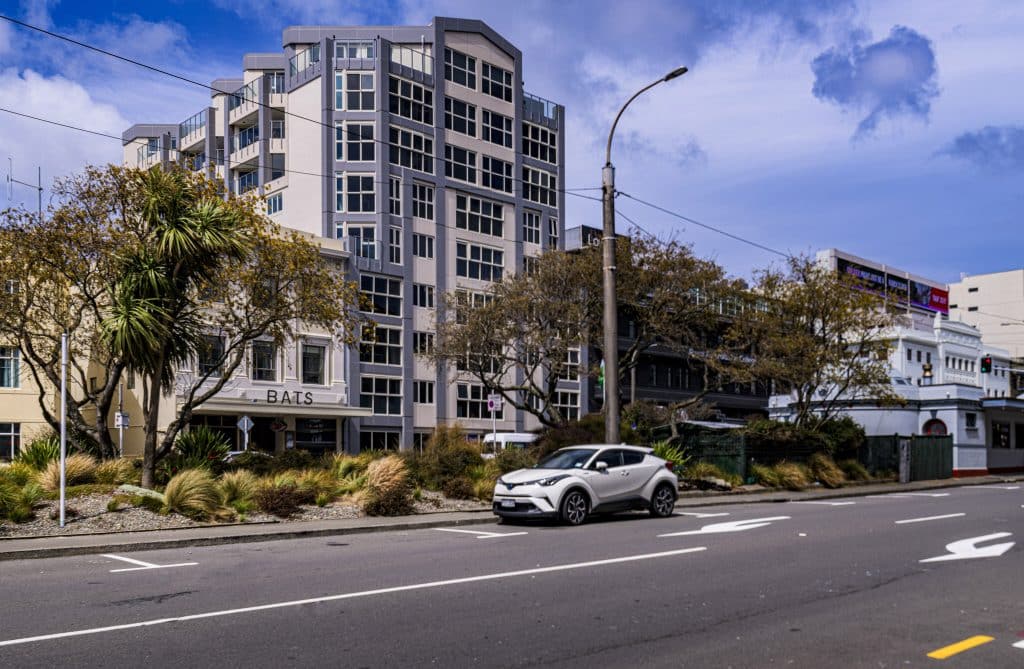
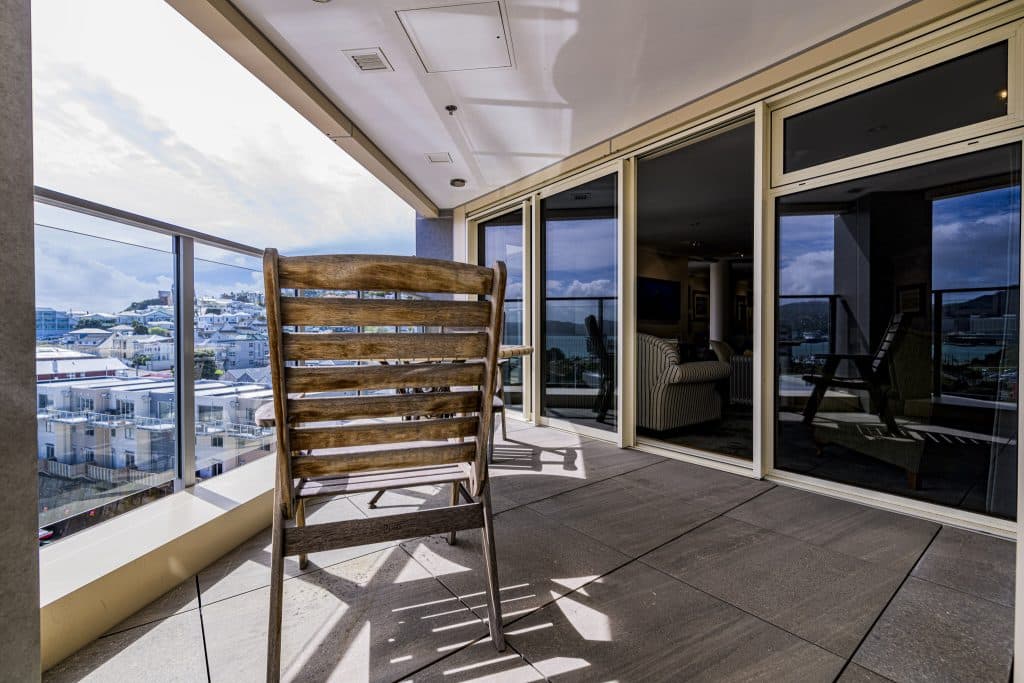
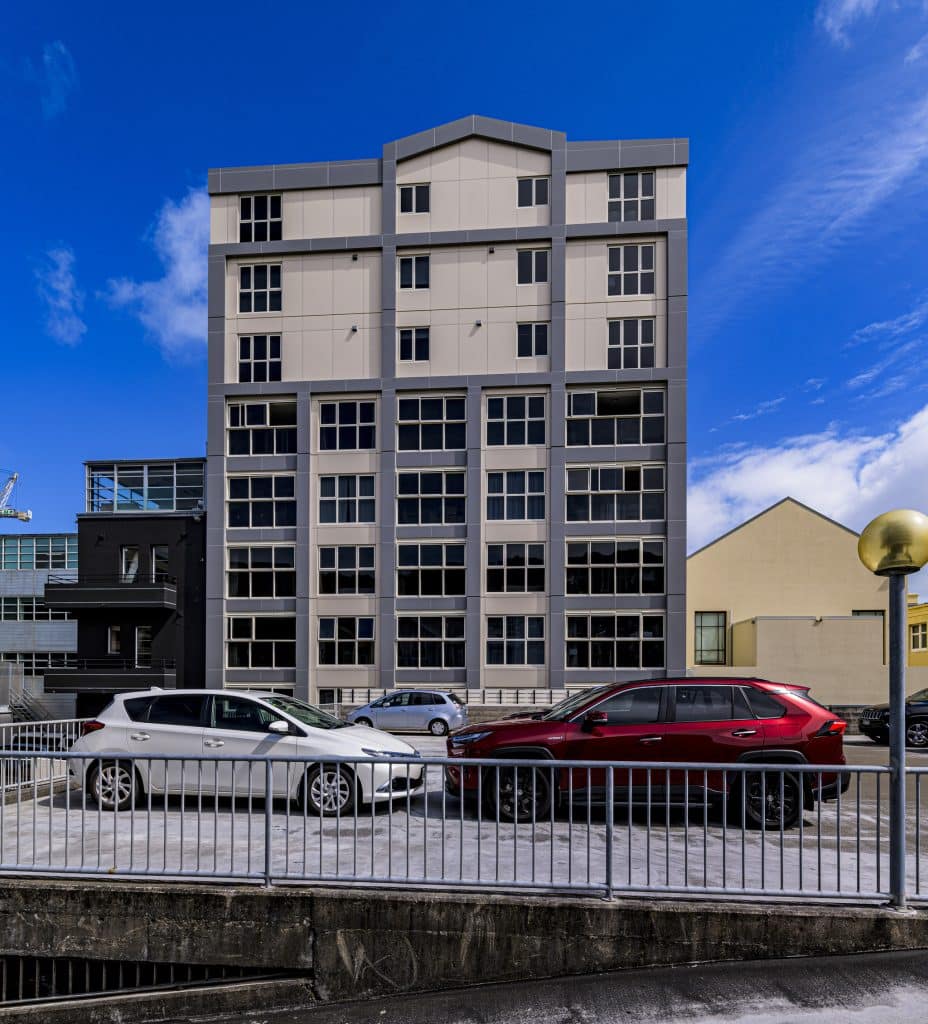
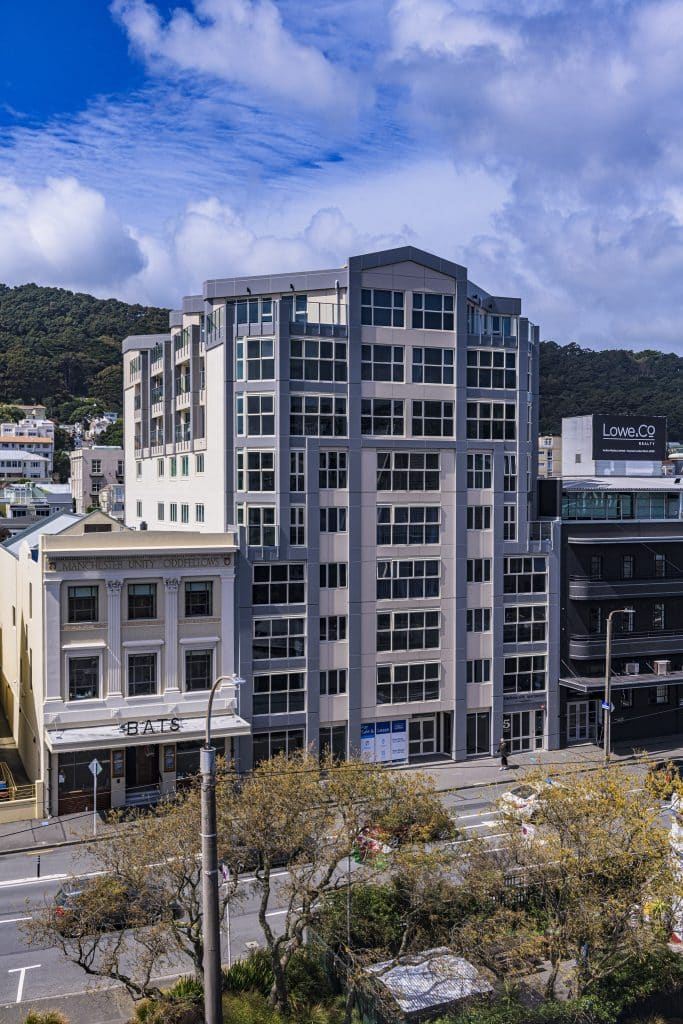
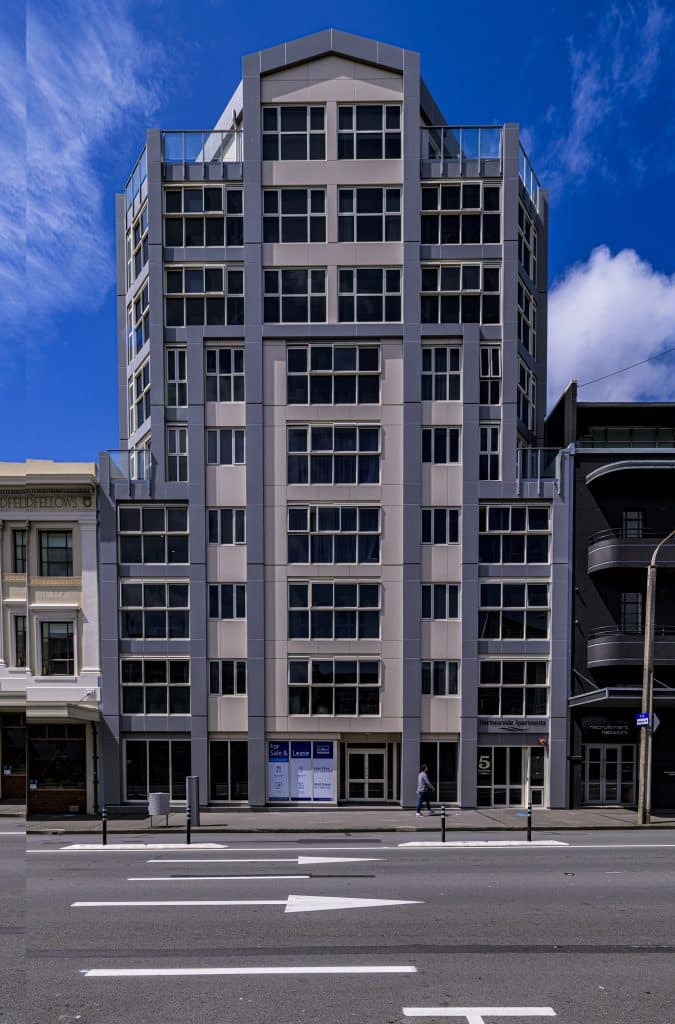
Need help with Project Management, Building Surveying, or Weathertightness Remediation? Feel free to reach out to Chris Ross at chris@prendos.co.nz or fill in the form below, and have us call you back.